Think of an automobile manufacturing facility. The complexity is outrageous. Dozens of departments, contractors, third-party warehouses. A concert of motion.
Automobile manufacturing is beautiful. An expression of the contemporary: Technology. Precession. Efficiency. It’s all built into the car that rolls off of the assembly line. Art in its modern form.
Who’s the best?
A study into the practices of the very best in automobile manufacturing companies insights respect.
Parts arrive at the manufacturing facility just seconds before being bolted onto the car as it moves down the assembly line. Sometimes the parts aren’t even in the building for cars that have already begun the process. Amazing. Zero error. Highly complex. And the best are doing it, without error for sometimes weeks or even months at a time. No stops. No mistakes. Smooth progress.
To be the best requires the master of many systems, technologies and business management practices. No one can do it alone. It takes a team.
The right approach
There’s far too much information in the automobile manufacturing process to keep in one’s head. So many places to make mistakes. And those mistakes result in waste. Cars that don’t start. Cars that leak when it rains. A lot like the cars that GM was building back in the 80’s. crap. junk. waste. Literally No-va.
Muda is Waste. All types of Muda (waste) are to be eliminated.
The best path through the automobile manufacturing workflow creates no waste, no wait times, no loss in efficiency.
Muda is controlled and eliminated wherever it exists. It’s an idea that rich and successful business practitioners think about often, as do we into our business. Muda exists and must be eliminated.
Efficiency matters
Efficiency is fundamental to doing anything well. Any person with a clear vision ultimately arrives at this notion, and builds structure around what needs to be done and the plan to do it.
Find a team who shares a plan and anything’s possible. But it takes a plan to succeed. We call this plan: standard operating procedure.
Standard operating procedures help to define and adhere to the most efficient workflow. Without them, Muda is sure to exist.
But not all standard operating procedures are the same. In fact, the variance between them is vast. Specific to a workflow. Build to a specification.
And even a topical review of different standard operation procedures shows that while there are differences among them, the commonalities are obvious. They work!
Huge communities. Entrenched. Paid experts stand ready to provide insights on the guiding principles. And indeed, theses types of experts work with us. They guide us in practice. They know what they are doing. They use field tested frameworks. No reason to reinvent the wheel.
Good standard operating procedures all have one thing in common. They are built to support a common, unified path through the best, most efficient workflow. Efficiency in practice. Structure that conforms to that process with zero impedance. As a business we must adhere to standard operating procedures.
Standard operating procedures can vary by type and surely will adapt to change along the way, but one thing is common throughout. One maxim. One defining principle. The fundamental approach in the way in which we run our processes is consistent throughout. A management philosophy. An identity. A core principle from which to operate.
Adherence to that principle is fundamental in the strictest sense to every action. This is why we succeed.
The process management system that we run successfully is Kanban.
Kanban :: business process management system. It’s the process management system used to create standard operating procedures. It’s how we run our business. Study kanban .
Kanban starts with a simple operating principle: eliminate Muda in each of its forms:
Different types of Muda
The seven wastes consist of:
- Overproduction. Manufacture an item before it is required. Overproduction is highly costly to a manufacturing plant because it prohibits the smooth flow of materials and actually degrades quality and productivity. The Toyota Production System is also referred to as “Just in Time” (JIT) because every item is made just as it is needed. Overproduction manufacturing is referred to as “Just in Case.” This creates excessive lead times, results in high storage costs, and makes it difficult to detect defects. The simple solution to overproduction is turning off the tap; this requires a lot of courage because the problems that overproduction is hiding will be revealed. The concept is to schedule and produce only what can be immediately sold/shipped and improve machine changeover/set-up capability.
- Waiting. Whenever goods are not moving or being processed, the waste of waiting occurs. Typically more than 99% of a product’s life in traditional batch-and-queue manufacture will be spent waiting to be processed. Much of a product’s lead time is tied up in waiting for the next operation; this is usually because material flow is poor, production runs are too long, and distances between work centers are too great. Goldratt (Theory of Constraints) has stated many times that one hour lost in a bottleneck process is one hour lost to the entire factory’s output, which can never be recovered. Linking processes together so that one feeds directly into the next can dramatically reduce waiting.
- Transporting. Transporting product between processes is a cost incursion which adds no value to the product. Excessive movement and handling cause damage and are an opportunity for quality to deteriorate. Material handlers must be used to transport the materials, resulting in another organizational cost that adds no customer value. Transportation can be difficult to reduce due to the perceived costs of moving equipment and processes closer together. Furthermore, it is often hard to determine which processes should be next to each other. Mapping product flows can make this easier to visualize.
- Inappropriate Processing. Often termed as “using a sledgehammer to crack a nut,” many organizations use expensive high precision equipment where simpler tools would be sufficient. This often results in poor plant layout because preceding or subsequent operations are located far apart. In addition they encourage high asset utilization (over-production with minimal changeovers) in order to recover the high cost of this equipment. Toyota is famous for their use of low-cost automation, combined with immaculately maintained, often older machines. Investing in smaller, more flexible equipment where possible; creating manufacturing cells; and combining steps will greatly reduce the waste of inappropriate processing.
- Unnecessary Inventory. Work in Progress (WIP) is a direct result of overproduction and waiting. Excess inventory tends to hide problems on the plant floor, which must be identified and resolved in order to improve operating performance. Excess inventory increases lead times, consumes productive floor space, delays the identification of problems, and inhibits communication. By achieving a seamless flow between work centers, many manufacturers have been able to improve customer service and slash inventories and their associated costs.
- Unnecessary / Excess Motion. This waste is related to ergonomics and is seen in all instances of bending, stretching, walking, lifting, and reaching. These are also health and safety issues, which in today’s litigious society are becoming more of a problem for organizations. Jobs with excessive motion should be analyzed and redesigned for improvement with the involvement of plant personnel.
- Defects. Having a direct impact to the bottom line, quality defects resulting in rework or scrap are a tremendous cost to organizations. Associated costs include quarantining inventory, re-inspecting, rescheduling, and capacity loss. In many organizations the total cost of defects is often a significant percentage of total manufacturing cost. Through employee involvement and Continuous Process Improvement (CPI), there is a huge opportunity to reduce defects at many facilities.
“Customers avoid waste in their purchase decisions, just like we do in our service to them.”
– Nick Hoffman
How we eliminate Muda
There are three ways that we eliminate Muda. Each of these is listed below.
1. Use the right resources
Use resources (tools) the right way. For example: there’s no fun in using Trello without knowing the keyboard shortcuts, trello.com/shortcuts .
In a similar vein of thought, knowing what it means to have good trello hygiene is a worthy pursuit.
If you’re going to do anything, be great at it. Be great in trello. Have good trello hygiene.
List of resources:
- Trello. Task management. Cards are items for execution under Kanban procedures.
- Slack. Chat. Support articles as messages. Trello cards and updates as messages.
- Gmail. Communication with external parties. Messages are forwarded to Slack and Trello where possible.
- CRM. Forward all emails to crm where possible.
- Shared Drives. Store files for both internal and external parties.
- Internal. Provision resources for customers, create new websites, etc.
- Main. Execute customer workflows and tasks
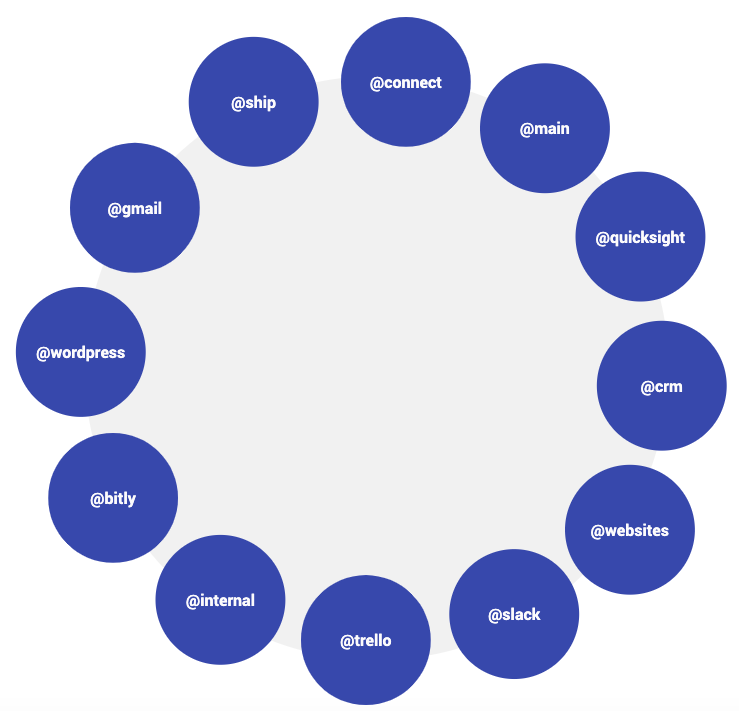
2. Adopt a common approach
Consistently implies that inputs are given to you in the right way (in good form), so that you can perform the job functions expected and produce the output intended. You are part of the process. A process that all starts with an understanding that you can only do one thing at a time and there’s no point to even think about anything other than that one thing that you are working on in that moment. In that moment is where your gifts are best expressed. It takes focus. It’s all about doing the work.
Imagine a cook. He grabs the piece of paper which includes the meals that need to be made. The ticket here is the same as a card in trello. It’s the instruction set, the task, the object of information, the inputs to do the work.
When you are ready to process a task, go to trello board and pull a card from the the left into the list that you are operating from. Drag the card with a tap or change the list from the detail view of a card to move it. Okay, you can now apply your focus and do the work.
Once you’re done with your work, move the card to the column to the right. This is where your work ends. You’re now ready to pull a new card and begin other work there. One task. One focus. Pure thought. Total signal. Zero noise.
Use boards correctly
Each of the items listed below are the usual, common, expected trello lists found across many trello boards (e.g. Internal Dev, Ops Support, etc.).
Pro tip: knowing how to use trello is the simplest way to look good at your job. Study the list below. Be in the right list at the right time. Think of each of theses items on the list below as steps in the workflow.
—-
Typical board workflow:
The steps below are found in most boards throughout Org.
Analysis.Doing
More is required in the way of inputs to accomplish the work required. Here, in this list, an Analyst is building, collecting, exploring the requirements. S/he builds and completes a checklist, fills in the custom fields, comments updates.
This such analysis is necessary for new items on the agenda or items of significance. It all starts with good requirements. What matters. SWOT. Many approaches. Organization matters. Analysis is art.
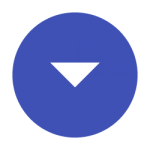
Analysis.Done
Any required inputs are included. Move the card here once requirements are included and Analysis.Doing is complete. This step is used by managers to check the quality the work performed in Analysis.Done by Analyst.
Once analysis is done, a Manager will move cards into the next step to the right, or instruct the Analyst to do so.
Note: This is the only list where the role assignment doesn’t match the name of the board. This is because Analysts work across several departments. Analysts are extra hands on deck to figure out complicated things.
Note: All roles will work in the Analysis lists at times, but not all cards will require analysis. Some cards are created in the very next list: Dev.Create, only if the analysis is done. Just think: would a drunk person understand my card? If not, then do the analysis first.
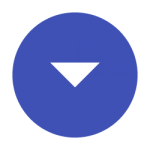
Dev.Create
All inputs are in place, and the card is ready to be picked up by the business unit for the work to be processed.
Think about a queue waiting to be processed. This can also be thought of as a state or staging area. The card will get pulled into the business unit for processing once the business unit is ready to process that task.
Note on Dev
above. This is used as an example class. It could’ve just the same been Video.Create or Auditor.Create. The role is the first word. The second word is the work that’s being done. This will make sense using the following template. These are functionally the same on each case. Visible on each role-specific board:
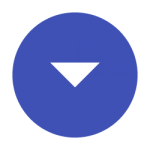
Dev.Dev
The business unit pulls from Dev.Create and is active, in this very moment, working on that card and executing the workflow required to complete that card. Think: welding a door on the car. The tool is in motion.
Exception? Use Dev.Backlog list
Dev.Backlog is used where inputs are required that are not available due to constraint or permission limitations.
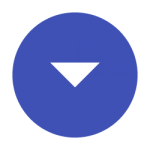
Dev.Review
Work is complete. Ready to be reviewed by an Analyst on the team. It’s still hot, let’s explore it for visual defects.
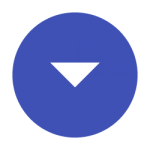
Dev.Testing
Performed by Analyst. Ensures that the work product meets the requirements specified in the card AND that the work is functional (e.g. does the button do what is should do?).
Pro tip: Use priority in review procedures. This will help to ensure enough focus is put on the review of quality of work.
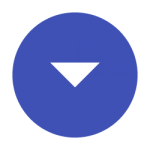
Dev.Done
Work for card is complete.
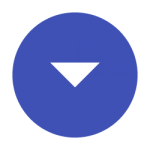
Acceptance.Doing
Manager reviews the work.
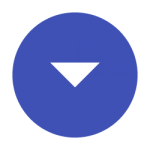
Acceptance.Done
Manager checks for product quality and prepares reports for Directors and other key stakeholders.
—-
Variance in boards
Boards can be different. Include different list names, and include very precise steps. The example above was taken from Internal Dev.
Red CAO Pipeline, for example includes some 86 lists within. Each a dedicated step for a dedicated person within the Auditor team.
No matter which boards you use in your job, or how they are named, the basic steps from Analysis, to Stage, to Dev, to Acceptance apply to all workflows.
General board lists
Analysis. Build the inputs.
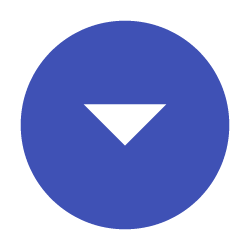
Stage. Ready for work. Inputs
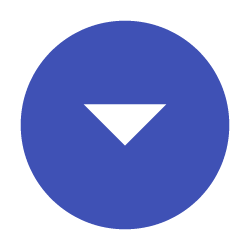
Dev. Doing the work. Functions
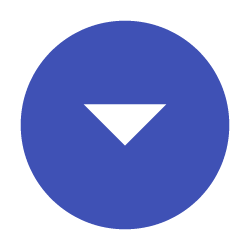
Acceptance. Review the work. Outputs
Notice the Italicized text above. Inputs, Functions and Outputs. No matter how complex, every system, either knowingly or unknowingly, operates from this this framework: Inputs, Functions and Outputs.
Trello boards are organized in a way that supports this flow.
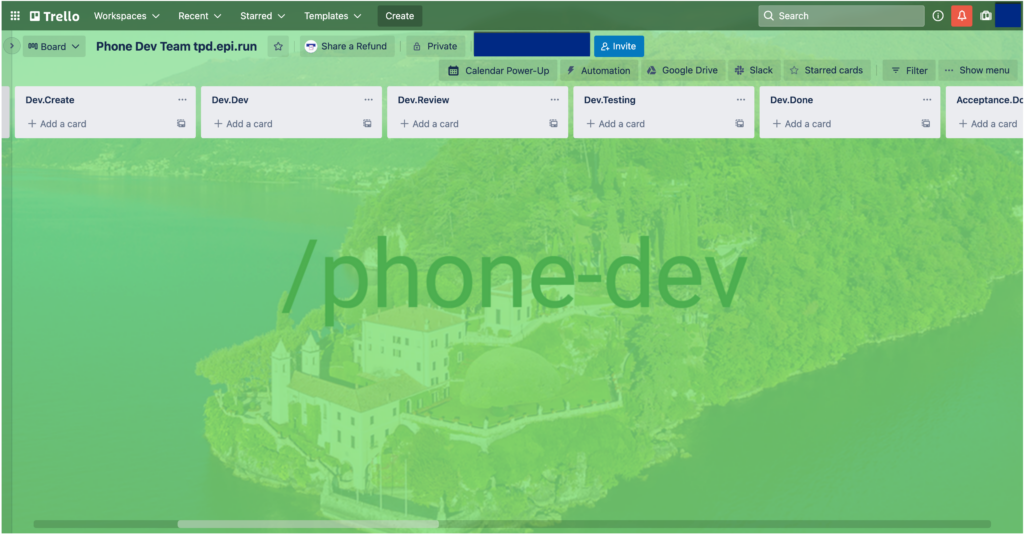
3. Hire the best people
This is where you come in. We’ve built the structure, and will continue to improve it over time, BUT the structure is only as good as the people using it. That’s why we strive to only hire the best. Including you.
The reason you are reading this article is because you are someone special. You matter. There’s greatness inside of you. Believe it. It’s true.
Your gifts will be appreciated here. Do great work. Work hard. Shine bright.
The only two things that matter are trust and hard work. Everything else is learned along the way.
– Nick Hoffman
Let’s be the most efficient team possible. Let’s provide service to each other, customers and beyond. Better than anyone. If you do it, be the best.
With these three operating principles, 1. Use the right tools, 2. Adopt a common approach, and 3. Hire good people, muda is eliminated and business thrives.
Let’s do big things together.